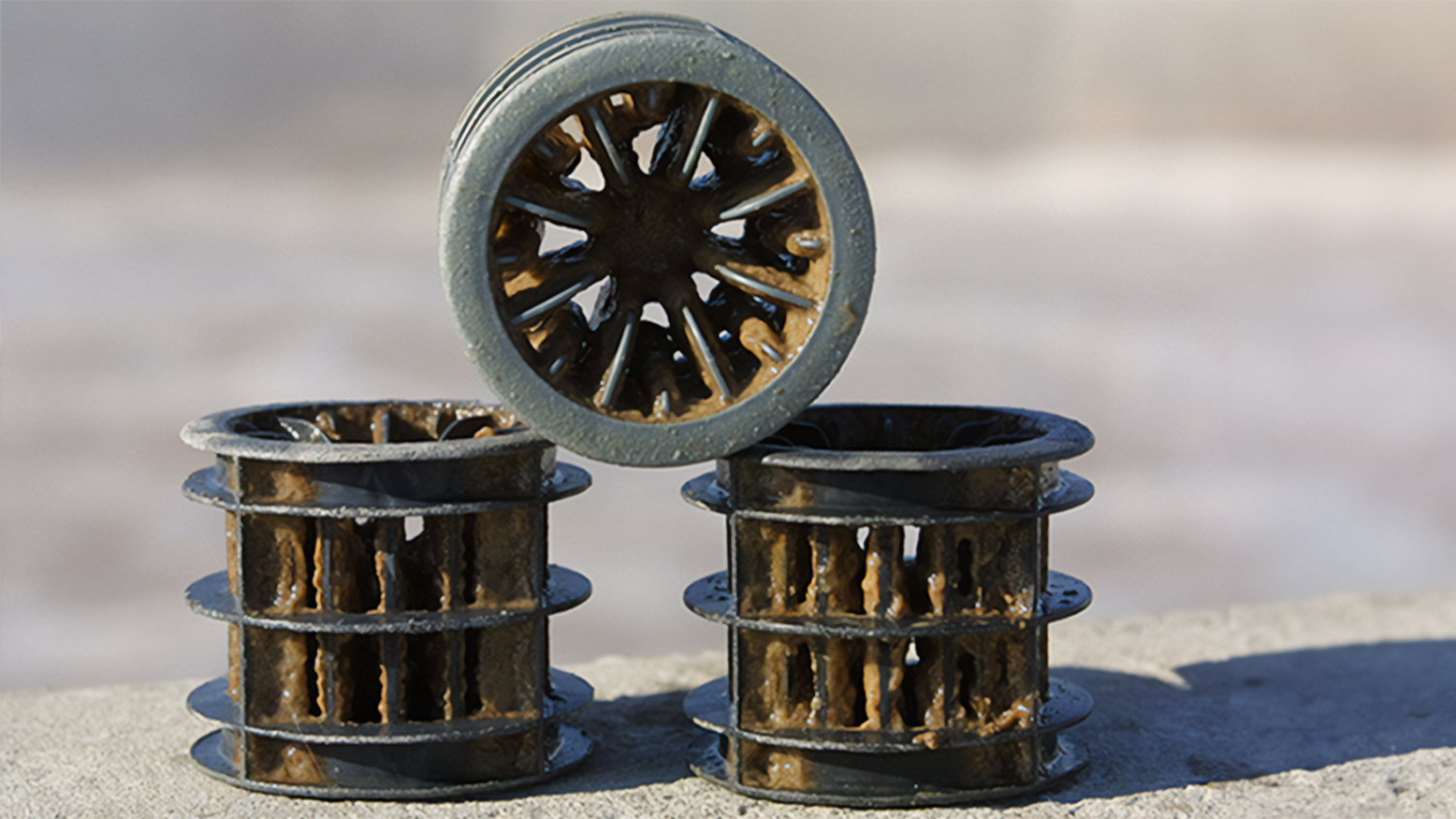
Not All MBBR Media is Created Equal – Selecting the Optimum Media for your Bioreactor
November 28, 2023
Moving Bed Bioreactors, or MBBR’s are quickly becoming common place in the treatment of industrial wastewater treatment in Australia. It is the inclusion of suspended media or carriers in the reactor that offer the MBBR process offers several advantages over conventional activated sludge or sequential batch reactor systems, particularly when dealing with high strength, or highly variable organic loads, and is also what gives MBBR its name!
The MBBR process is ideal for sectors such as the beverage industry, petrochemical, pulp and paper or the treatment of industrial liquid wastes and because of the rise in popularity of the technology, the global water market has seen an explosion of different MBBR media suppliers. The challenge for designing an effective treatment process is selecting the right media type.
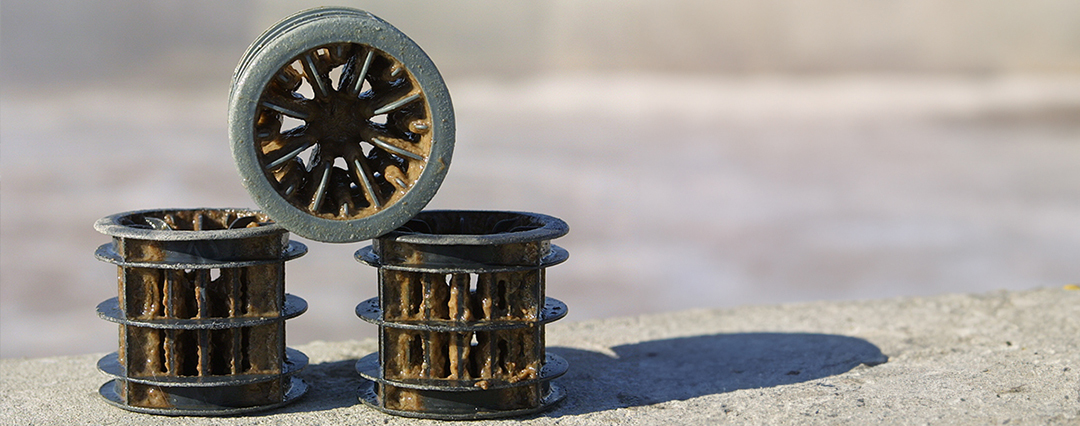
Some mass produced MBBR media utilises an extrusion manufacturing process with polypropylene media. This allows the manufacture of a relatively low-cost product, but the smooth surface prevents efficient attachment of the biofilm resulting in a large fraction of the surface area being wasted.
The unique molded design of the patented FlooBed® MBBR material from Flootech offers several significant advantages over conventional extruded MBBR media. The roughed surface of the molded design is able to maintain a significantly greater biomass population per m2 of media surface area, allowing reactors to operate with lower fill rates, when compared with conventional extruded chips or structured carriers with the same carrier specific surface area. The higher specific attachment efficiency means that FlooBed® carriers can be more open, such as the 438 series carrier. These open carriers are also more durable, with thicker material and the ability to
appropriately strengthen the outer edges to reduce the effects of abrasion/wear. The FlooBed® media is proven to operate at media replacement rates of < 5% per annum, compared with some conventional imported extruded and also sponge type carriers which can require replacement rates exceeding 30%.
Open media designs minimise the effects of media blocking/scaling which are a major issue with extruded media and one of the main challenges for operating MBBR systems on industrial effluent. Blocked media is often unable to remain in suspension, sinking to the bottom of the reactor and removing any attached biomass from the treatment process.
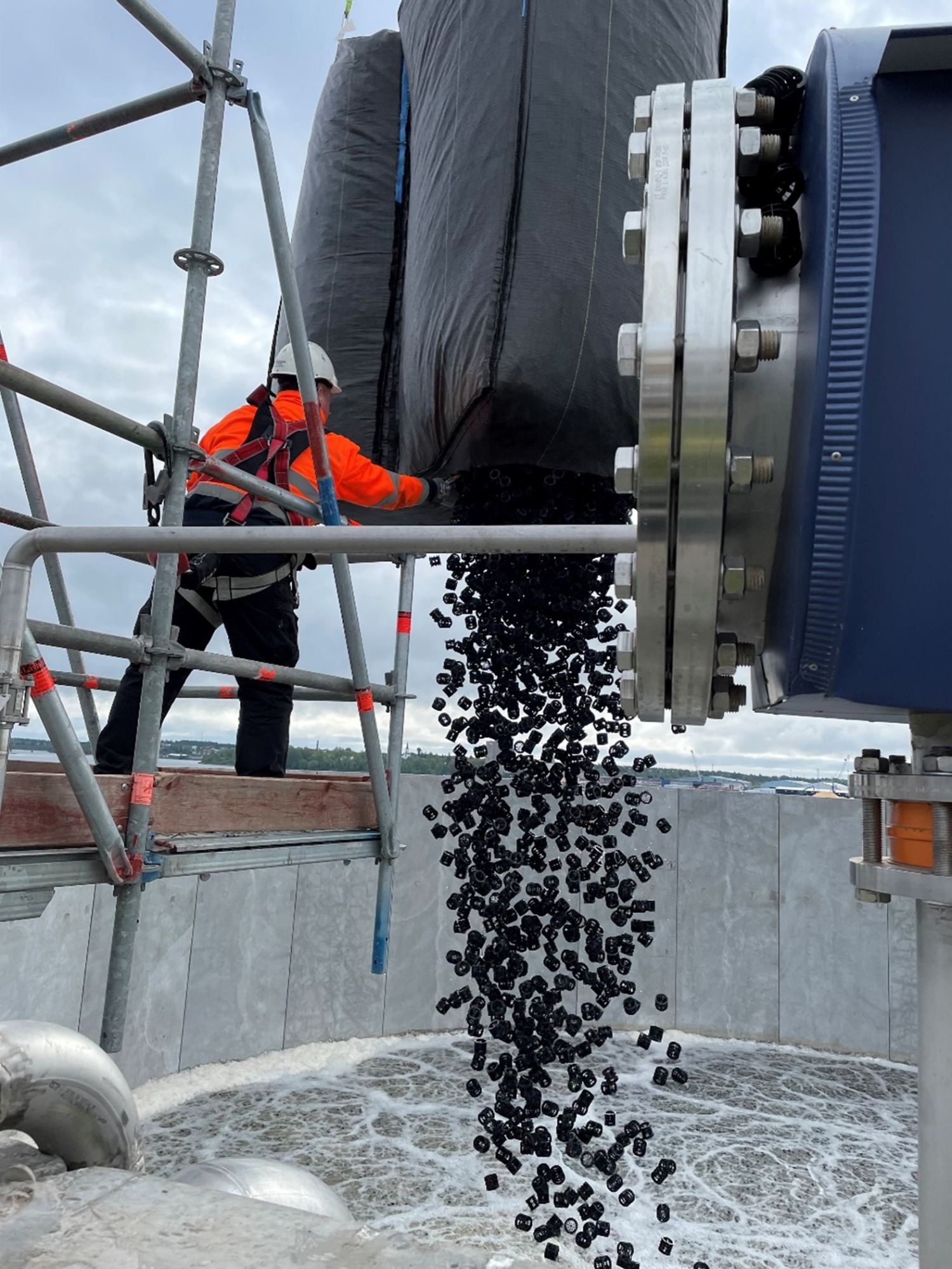
In difficult applications, the durable FlooBed® can be cleaned in situ through the proprietary Mammoth® airlift pumping system. Conventional extruded media cannot withstand the shear forces within the pumping process, so blocked extruded media can rarely be recovered.
The net result in costs to construct and operate an MBBR system utilising molded media types such as FlooBed® is significant. The use of less expensive extruded media could result in 20-year life cycle costs 3 – 3.5 times higher when compared with a high-quality molded product.
The Hydroflux team in co-operation with Flootech have been designing and constructing large MBBR systems across Australia and New Zealand for the past 25 years. Our focus since the inception of Hydroflux and in our collaboration with Flootech is the development of the most economically and environmentally sustainable MBBR systems, which includes the utilisation of MBBR media at its core.
About the Hydroflux Group
The Hydroflux Group aims to deliver the highest level of engineering and scientific know-how to the emerging issues of sustainability, climate adaptation and environmental protection with a specific focus on water and wastewater.
As part of its vision and mission, Hydroflux has always taken its climate responsibility seriously. In 2022, Hydroflux became Australia’s first water treatment and technology company to achieve Climate Active carbon neutral certification for its organisation and products. It knows that partnering with customers and clients is the most significant impact it can have in its journey. The Group employs over 100 staff and operates throughout Australia, New Zealand and the Pacific Islands, with office locations in Sydney, Melbourne, Brisbane, Perth, Auckland, Suva and Portsmouth.
Up Next
Fonterra Upgrades WWTP with Advanced HyDAF Systems.
Categories
- Tradeshows
- Climate
- Community Engagement
- Corporate Announcements
- Group News
- Newsletters
- Product News
- Project Announcement