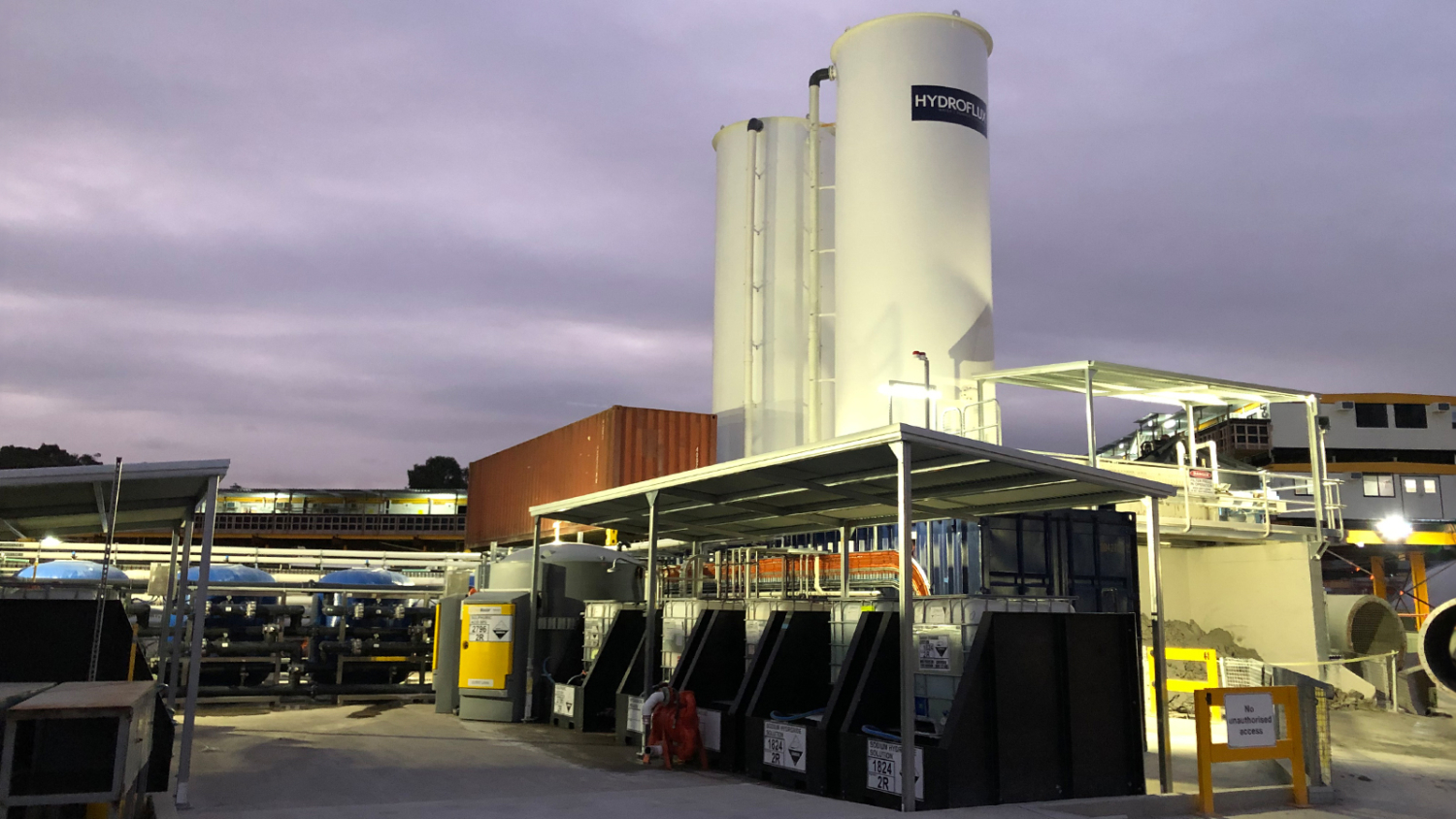
Hydroflux: Navigating the Depths of Efficient Wastewater Treatment for Tunnelling Projects
July 27, 2023
Australia’s Eastern seaboard is in the midst one of the largest infrastructure development cycles in recent history. This infrastructure boom has been driven by government investment into road and rail developments. Significant projects in Brisbane, Sydney and Melbourne are all underway to improve sewer, road and rail networks within the region.

Much of this work involves tunnelling underground to generate faster routes for roadways, rail lines and piping systems. As with any construction work, tunnelling produces wastewater on site which needs to be treated before it can be discharged to the sewer or the environment. The release of groundwater, as well as the relatively high volume of water generated by road-headers and tunnel boring machines combine to form a mixture of wastewater that can vary from site to site.
Due to the large scale of the projects, large volumes of water may need to be discharged to the environment and treating to the traditional “Blue Book” values of pH 6.5 – 8.5, TSS < 50mg/L and FOG < 10 mg/L that may apply to smaller surface construction works is not sufficient. Tunnelling sites must also comply with strict requirements for heavy metals, hydrocarbons, sulphides, and nitrogenous compounds to comply with Australian and New Zealand Guidelines for Fresh and Marine Water Quality (ANZECC) 2000 guidelines for waters discharging into the environment.
Unlike general surface works, tunnelling presents a wide range of additional challenges for managing and treating the wastewater. Primarily, the water generated by the tunnelling works is very heavily loaded with a wide range of solids in comparison with other types of construction. Heavy, rapidly settling silt and sand collect in sumps, sedimentation ponds and balance tanks which can then hold back the water flow. At the same time, high concentrations of colloidal clays, grout and bentonite fines do not settle without chemically conditioning the wastewater prior to a robust clarification process. Often, filtration is then required as a final protective barrier against residual solids passing through the treatment process, but these can become overloaded if upstream treatment steps are not correctly designed with optimum chemical conditioning and appropriately robust clarifiers.
To throw a spanner in the works, tunnelling projects will often run through a large area. The water generated by the works can change significantly as the project progresses, and the types and concentrations of industrial contaminants and groundwater flow rates will vary throughout the project.

More recently, Per and Polyfluoroalkyl Substances (PFAS) contamination of groundwater generates additional challenges for the water treatment system due to the changing regulatory requirements for handling these substances.
Hydroflux engineers have successfully designed and built water treatment plants treating to ANZECC guidelines for the past three decades. Having worked on a variety of different tunnel constructions and supported the tunnelling industry with tailored designs and ongoing operational support, a wide range of solutions have been used with varying degrees of success due to the variability of conditions of the different sites.
From our experiences, the key to hassle free wastewater treatment on tunnelling projects is:
- Simple, staged treatment processes that target specific issues one at a time;
- Conservative, robust designs to handle the variable and demanding conditions on site;
- Flexibility and modularity in the design to allow easy modification and upscaling; and,
- A high degree of automation to minimise operator input adapt to changing conditions.
Above all it is important to highlight the dangers in attempting to oversimplify the treatment process. Basic clarifiers and filtration systems available for hire lack specific design considerations and often fail quickly. Fine filtration technologies such as Ultrafiltration are an excellent final barrier to ensure compliance, but they are not designed to take high solids loads.
There are several risks to a poorly designed treatment plants for tunnelling construction. Operating costs on tunnelling sites rapidly spiral out of control when water treatment plants are not able to cope with the challenges presented by the untreated tunnelling water. These costs can include;
- Water treatment plants requiring 24/7 operator attention to keep them running.
- Excavator equipment on permanent hire to manage the solids depositing in ponds or tanks.
- High sludge disposal costs due to undersized or ineffective dewatering systems.
- High cost for spare parts for plants utilising Ultrafiltration technology, due to ongoing membrane replacements.
Although tunnelling projects present challenges to water treatment companies, they also present rare opportunities. There is real potential to add value and save tunnelling contractors significant amounts of money across the lifecycle of the project by involving a professional water treatment company such as Hydroflux in the tender stage.
Investing in a robust water treatment solution provides peace of mind, which enables tunnelling contractors to get on with the job of connecting our ever-expanding cities.
About Hydroflux
The Hydroflux Group aims to deliver the highest level of engineering and scientific know-how to the emerging issues of sustainability, climate adaptation and environmental protection with a specific focus on water and wastewater.
As part of its vision and mission, Hydroflux has always taken its climate responsibility seriously. In 2022, Hydroflux became Australia’s first water treatment and technology company to achieve Climate Active carbon neutral certification for its organisation and products. It knows that partnering with customers and clients is the most significant impact it can have in its journey.
The Group employs over 100 staff and operates throughout Australia, New Zealand and the Pacific Islands, with office locations in Sydney, Melbourne, Brisbane, Perth, Auckland, Suva and Portsmouth.
Up Next
Cress newsletter – July 2023
Categories
- Tradeshows
- Climate
- Community Engagement
- Corporate Announcements
- Group News
- Newsletters
- Product News
- Project Announcement